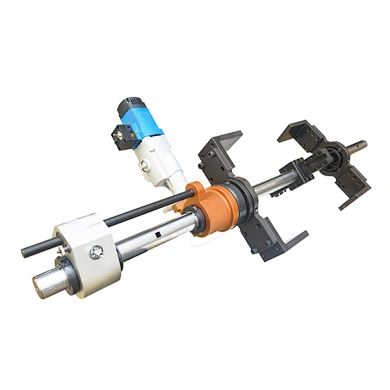
# On-Site Flange Machining: Efficient Solutions for Industrial Maintenance
## The Importance of On-Site Flange Machining
In today’s fast-paced industrial environment, downtime can be extremely costly. On-site flange machining has emerged as a critical solution for maintenance teams looking to minimize equipment downtime while ensuring precision repairs. This specialized service brings professional machining capabilities directly to your facility, eliminating the need for disassembly and transportation of large components.
## What is On-Site Flange Machining?
On-site flange machining refers to the process of repairing, resurfacing, or modifying flanges at their installed location using portable machining equipment. Unlike traditional methods that require removing flanges and sending them to machine shops, this approach allows for:
– Immediate repairs without disassembly
– Significant cost savings on transportation
– Reduced downtime for critical equipment
– Precision machining in the field
## Common Applications of Portable Flange Machining
Industrial facilities across various sectors benefit from on-site flange machining services:
### Power Generation Plants
Maintaining proper sealing surfaces on turbine flanges and heat exchanger connections is crucial for operational efficiency and safety.
### Oil and Gas Facilities
Pipeline flanges, vessel connections, and compressor stations often require in-situ machining to maintain integrity without shutting down entire systems.
### Chemical Processing Plants
Corrosion-resistant flange surfaces need periodic refurbishment to prevent leaks in hazardous environments.
### Water Treatment Facilities
Large diameter pipe flanges in water distribution systems benefit from on-site machining when replacement isn’t practical.
## Advantages Over Traditional Methods
On-site flange machining offers several distinct benefits compared to conventional repair approaches:
### Time Savings
By eliminating the need to remove and transport components, repairs can be completed in a fraction of the time required by traditional methods.
### Cost Efficiency
Significant savings are achieved through reduced labor hours, elimination of transportation costs, and minimized production downtime.
### Precision Results
Modern portable machining equipment delivers accuracy comparable to stationary machine shops, often within 0.001 inches.
### Safety Improvements
Working on installed components reduces risks associated with heavy lifting and transportation of large industrial parts.
## The On-Site Machining Process
Professional on-site flange machining typically follows these steps:
1. Initial assessment and measurement of the flange surface
2. Setup of portable machining equipment
3. Precision machining to restore flatness and surface finish
4. Quality verification using precision measuring instruments
5. Final inspection and documentation
## Choosing the Right Service Provider
When selecting an on-site flange machining company, consider these factors:
– Experience with your specific industry and equipment types
– Range of portable machining capabilities
– Certifications and safety records
– Response time and availability
– Quality assurance processes
## Future Trends in Field Machining
Keyword: On-site flange machining
The field of on-site flange machining continues to evolve with technological advancements:
– Integration of digital measurement and documentation systems
– Development of more compact and versatile portable machines
– Increased use of automated machining processes
– Enhanced data collection for predictive maintenance programs
By adopting on-site flange machining solutions, industrial facilities can maintain operational efficiency while significantly reducing maintenance-related downtime and costs.